With a vision to always act ethically towards the environment, whilst creating value for our stakeholders, we are always looking for ways to improve how we do business. In recent months, we’ve turned our attention to our warehousing operation.
For the last three years, we’ve contracted out our warehouse services, utilising space in Preston operated and maintained by an external company. Rather than commit to another lease term Pelta Supply Chain Manager Tony Raven led the project to bring our warehouse closer to home and under our own management.
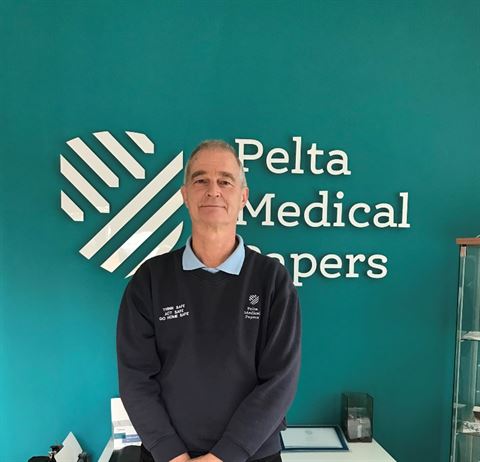
Having worked at the Beetham mill for 29 years, Tony has operated in a number of different roles including production, technical and shift management. Over the years he has made his way up the ranks and today operates as our Supply Chain Manager.
Observing an increase in the demand for quality, Tony supports the production function at the mill to ensure we are suitably equipped to meet the requirements of our customers.
In June of this year, Tony secured two warehouse units at the Mainline Industrial Estate in the neighbouring town of Milnthorpe. We began transferring stock on June 6th from our Preston hub and now operate solely from our new base manned by our own personnel.
In addition to significantly reducing the mileage used for transportation, we now also possess better quality control of up to 2,000 tonnes of stock having secured the lease for an additional unit as of September 23rd.
Currently, we despatch around 10 loads a week to customers from our new base with on average two stock loads daily making the trip from Beetham to Mainline. Moving our warehouse closer to home has allowed us to significantly reduce the environmental footprint used by trucks to transport our goods from mill to warehouse.
Tony Raven, Supply Chain Manager at Pelta Medical Paper commented:
“Because of the very tight deadline we had to set these new warehouses up, Leon Lachmann (Logistics Manager) and the team at Mainline did a great job moving 2000 tons of stock from Preston to Mainline. It was a great example of team collaboration and working to solve problems together, a Pelta value, and as a result, everything is now running smoothly. We will continue to improve our Environmental footprint whilst looking for new Logistics providers to service our operation at Mainline.”
This is just one of the actions we have taken to improve our carbon footprint at Pelta Medical Papers. We also recently worked with waste contractors Cumbria Waste in order to optimise our waste management process. Learn more about what’s happening at Pelta by reading our latest news.